As engineers know all too well, a cable is much more than a convenient way of connecting two electronic devices: it is also a complex passive circuit with its own resistance, capacitance, and inductance. A typical cable in a demanding aerospace or military application, such as the 10G Base-T Cat 6a Ethernet cable shown in Figure 1, contains multiple parts.
Although customers might wish for a cable of unlimited length, two reasons limit the spool length of real-world products: Manufacturing materials and practical manufacturing constraints. To ensure the best quality cables, multiple tests are performed to verify the cable’s effectiveness.
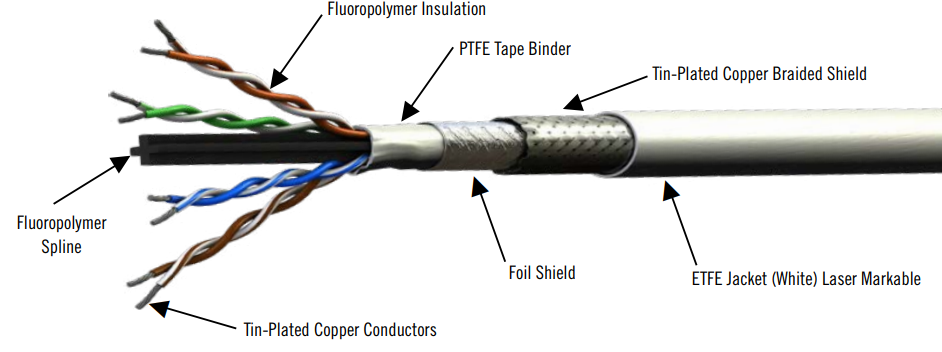
Common Cable Manufacturing Challenges
The finished cable assembly must meet the mechanical and electrical performance requirements for the end application. Each part of a cable represents a potential point of failure, which can occur at any point along its length. If testing detects a failure, the flawed section of the cable is removed and the two sections are retested. Complex cables have more potential failure mechanisms and shorter maximum cable lengths.
As depicted in Figure 1, kinks or stray wires in the primary conductors can cause issues such as out-of-spec outer diameter (OD), and electrical issues like high attenuation or return loss. A strand poking through the wire insulation can also cause a spark test failure.
Many factors can result in a primary conductor insulation failing the spark test such as contaminants (FOD), the processing of individual primary wire insulation, which can vary slightly depending on equipment setup, the operator, and batch (lot) of fluoropolymer and things like daily temperature.
The outer braid shield is where a cable braid consists of numerous small wires, each on an individual tiny bobbin or spool. The wire braid shield is applied after (over) the foil braid. If a wire breaks during the braiding operation, the cable must be cut at that point to replace the bobbin before continuing the braiding process. A new spool is then started; this also applies if an individual bobbin runs out.
The overall jacket undergoes a 100% spark test that looks for small imperfections in the overall cable jacket. The outer braid is grounded and the cable is run through a bead tester that has a high voltage (typically 3.0 kV) applied to it. Any microscopic pinhole or flaw in the cable jacket will cause a spark, resulting in an automatic shutdown of the test and the removal of the flawed section.
The final test ensures that the finished cable meets its specified electrical performance requirement. For example, a CAT 6a (four-pair) Ethernet cable must pass Category 6a testing, which includes near-end cross-talk (NEXT) and insertion loss. If the cable fails any requirement, the cable is retested to isolate the failure to a certain area of the cable. In that event, the section is removed (cut out) and the cable is retested. It is possible that the entire spool could be suspect and ultimately destroyed.
Common Cable Manufacturing Challenges
The finished cable assembly must meet the mechanical and electrical performance requirements for the end application. Each part of a cable represents a potential point of failure, which can occur at any point along its length. If testing detects a failure, the flawed section of the cable is removed and the two sections are retested. Complex cables have more potential failure mechanisms and shorter maximum cable lengths.
POTENTIAL MATERIAL FLAWS